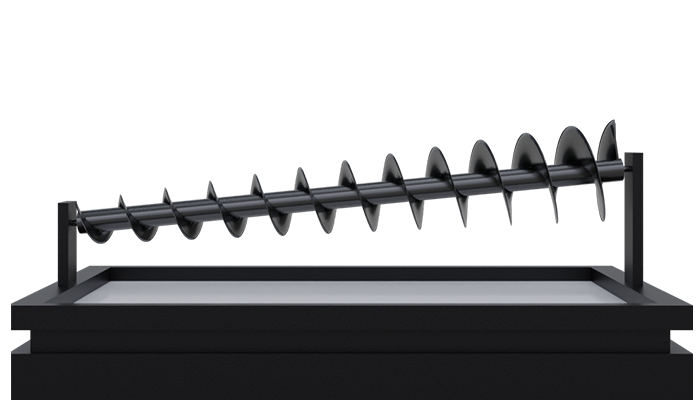
You might never have seen the above tool in your urban life, but the Archimedes Screw is one of the oldest tools that is still widely used in today’s world. The helical shape allows it to carry stuff up or down when rotated. This engineering masterpiece dates back to the 3rd Century BCE. The Egyptians used the screw to transfer water from the Nile. It is efficient in carrying a large amount of water across different elevations. Just to show you how it works, this small GIF should suffice.

Modern Applications
Today Archimedes screw is predominantly used in irrigation, transferring of water from drains, etc. But there is some interesting and rare use as well.
Amphibian Vehicles
One of the interesting uses of Archimedes screw is a screw-propelled vehicle, mostly amphibians, where the cylinder can act as a float as well.
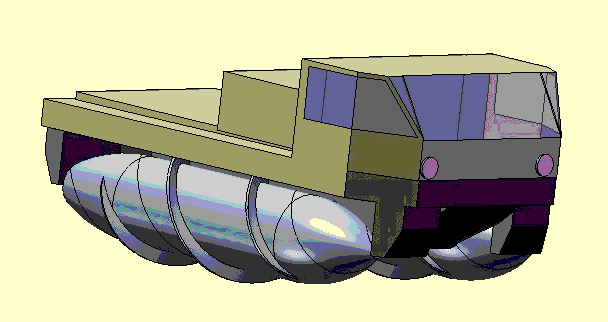
Screw Propelled Ships
Another interesting and heavy-duty use is to drive boats or ships even. SS Archimedes was the first ship ever to use screw propellers.
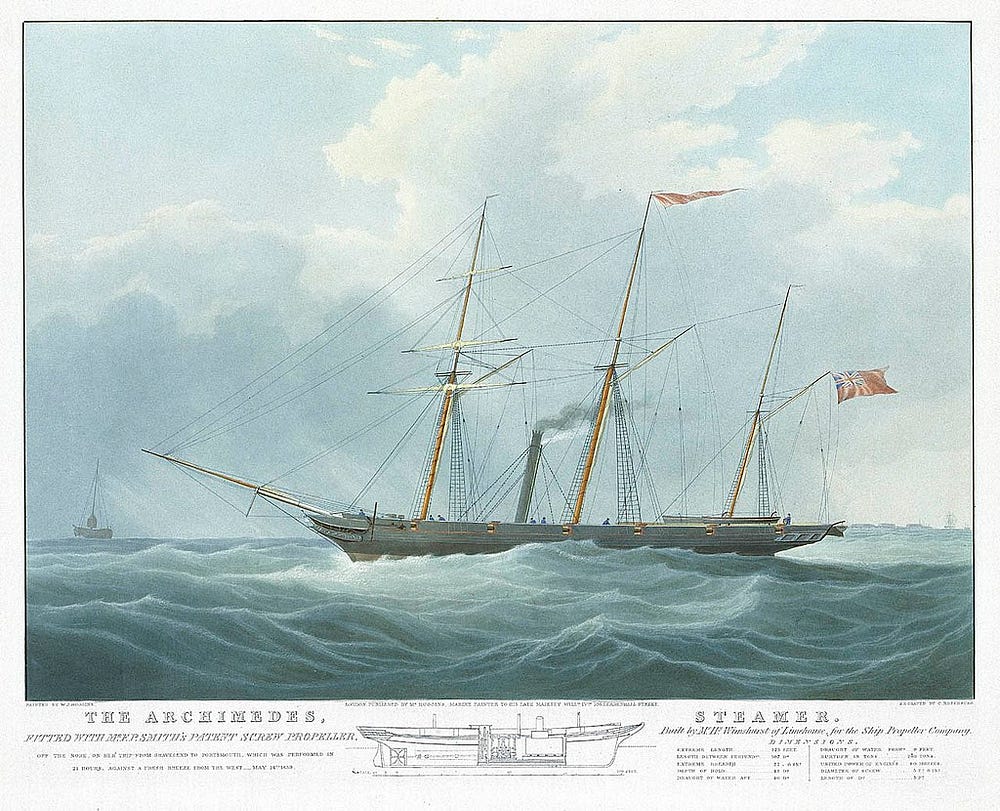
Screw Turbines
Screw turbines use the Archimedes screw to convert water’s potential energy into work, much like any other turbine. Such turbines are still used in Canada, the United States of America, and the United Kingdom.
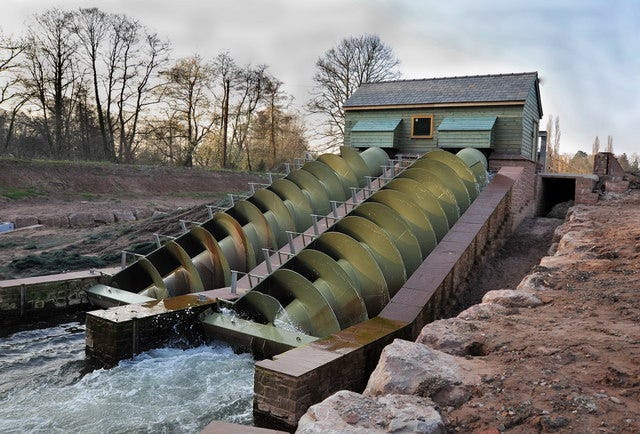
For one such interesting application, Fabheads set out to explore the possibility (and ended up fabricating) Continuous Carbon fiber-based Archimedes screw. Let’s first understand why is that unique.
Traditional Archimedes Screw manufacturing
The screws used by heavy-duty industries are made out of metal or specifically, steel. They are manufactured using a combination of processes such as —
- Welding
- Sheet metal fabrication
- Forging
- Machining
Depending on the dimensions of the screw, it can take from a month to several months to complete one screw in production, much more during the prototype or development stage.
Metal components also have the disadvantage of corrosion, especially in a marine or humid environment. Even without corrosion, metal parts have a preset fatigue life which limits the usage in high-cycle applications. To overcome these limitations, Fabheads set out to develop a Carbon fiber-based Archimedes screw.
Challenges of Carbon Fiber screw
If you are conversant with continuous carbon fiber fabrication then you are aware of the complexities associated with it, especially with complex shapes. The fiber direction needs to stay in the direction of the highest strength/stiffness requirement.
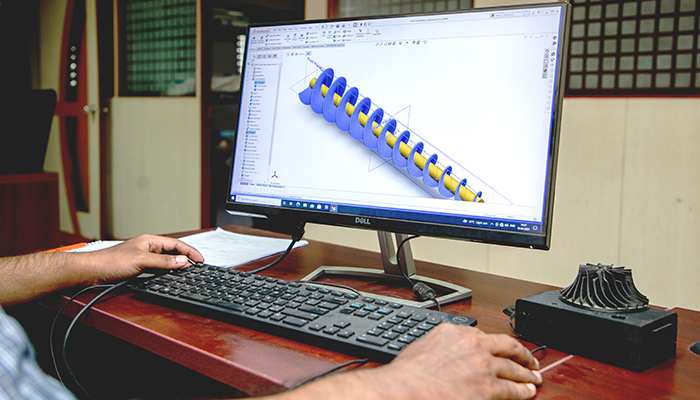
1. Maintaining fiber orientation
In the case of the Archimedes screw, the screw portion requires strength mainly in the radial direction, which will give the screw fin the ability to take the bending caused due to propulsion force (if the screw is used for propulsion).
Along with this, the tangential direction is equally important to have high stiffness to not deform under any propulsion force. As a result, carbon fiber is to be laid in two perpendicular directions, while going in a helical path.
2. Shaft-screw interface
Along with the fiber layup issue, the screw portion is supposed to move along with the shaft i.e. the power goes through the shaft to the screw portion. That means the shaft screw interface needs to be strong and leakproof as well.
3. CF over-wrap on the shaft
Plus, to avoid corrosion an over-wrap of carbon fiber was also desired over the metal shaft.
4. Complex mould shape and fin profile
Another challenge is to have a mold/template surface for a layup which is the negative of a screw. With traditional manufacturing, this means either welding together several parts or milling out huge amounts of material from a big block, both of which take a lot of time, effort, and budget.
Along with all this, the screw portion (fin) has a radial outward convex profile required for proper fluid flow over the Archimedes screw.
The shape, strength and stiffness challenges of carbon fiber Archimedes Screw are something you don’t even see in composite rocket structures.
– Abhijeet Rathore, CTO Fabheads
How Fabheads changed the game?
Fabheads has taken Archimedes Screw manufacturing to the next level with the help of our in-house continuous fiber printers — FibrBots. We have successfully fabricated a continuous carbon fiber-based Archimedes screw using 3D printing-assisted fabrication.
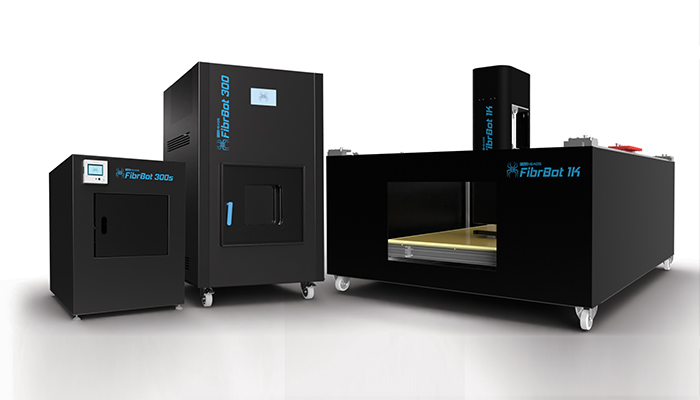
The lead time for this was less than a week (for the first part) which in itself is a remarkable feat. The use of 3D printing and carbon fiber improves the screw functionality when compared to the regular screws available in the market.
How did Fabheads do it?
The Archimedes screw is undoubtedly one of the most complex structures we have ever fabricated with our 3D printers
– Akshay Ballal, CPO Fabheads
With our in-house developed, patented carbon fiber 3D printer, we managed to make the Archimedes screw with remarkable precision, while maintaining both the strength and stiffness of the screw. Revealing the exact process used is beyond this blog’s scope and restricted by non-disclosure. But we’ll go through some of the steps —
- The fibers are oriented along the radial and tangential directions as required using our proprietary 3D printed assisted fabrication. Fiber continuity is piece-wise maintained from the very bottom of the shaft to the very top, with fiber orientation changing on a helical path.
- The shaft is piece-wise over-wrapped with carbon fiber. The over-wrap continuously joins with the screw fins (with fiber continuity maintained). This ensures a smooth load transfer from the shaft to the screw fins while maintaining the water-tight screw-shaft interface. Also because the shaft is now over-wrapped, the metal shaft is safe from corrosion. This over-wrap was, again, done using our 3D printing-assisted fabrication processes.
- The required molds were 3D printed with Fabheads in-house printers. For the varying radius of the parts, 3 separate molds were printed to ensure quicker fabrication. These 3D printed molds were a significant reason for the overall lesser fabrication time
- The fin geometry detail was also precisely fabricated with the special processes used by Fabheads. A special grinding machine was developed just to enable finishing operations with a linear motion while tapering inwards / outwards as per the shape of the screw.
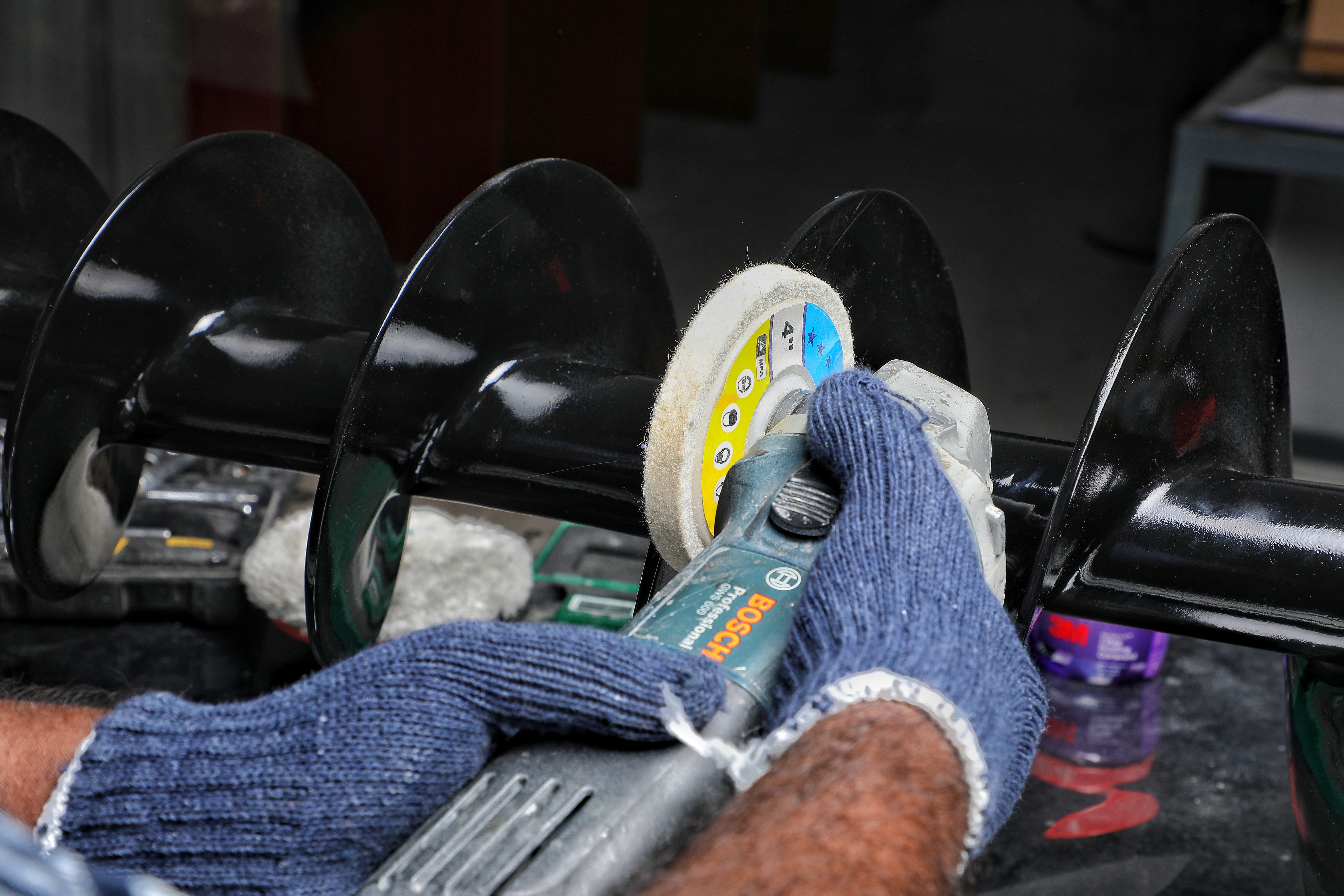
Advantages of composite manufacturing
The use of carbon fiber resulted in a significant weight reduction. It is ~30% lighter than a typical aluminum screw. Most of these screws are driven by motors to speed up the transfer process. A lightweight screw also helps in improving the overall power utilization. Carbon fiber is corrosion-resistant, which means the screw is perfect for water-based applications. It improves the longevity and durability of the screw.
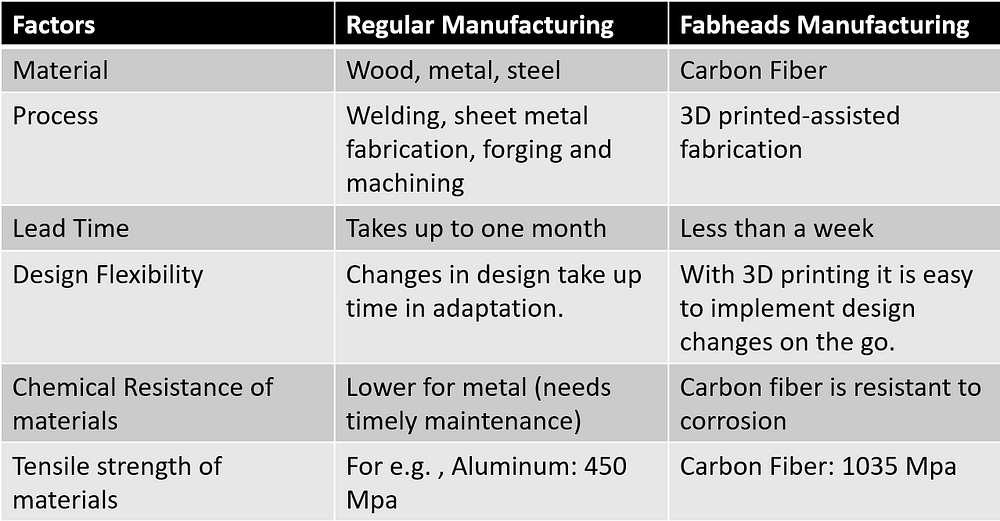
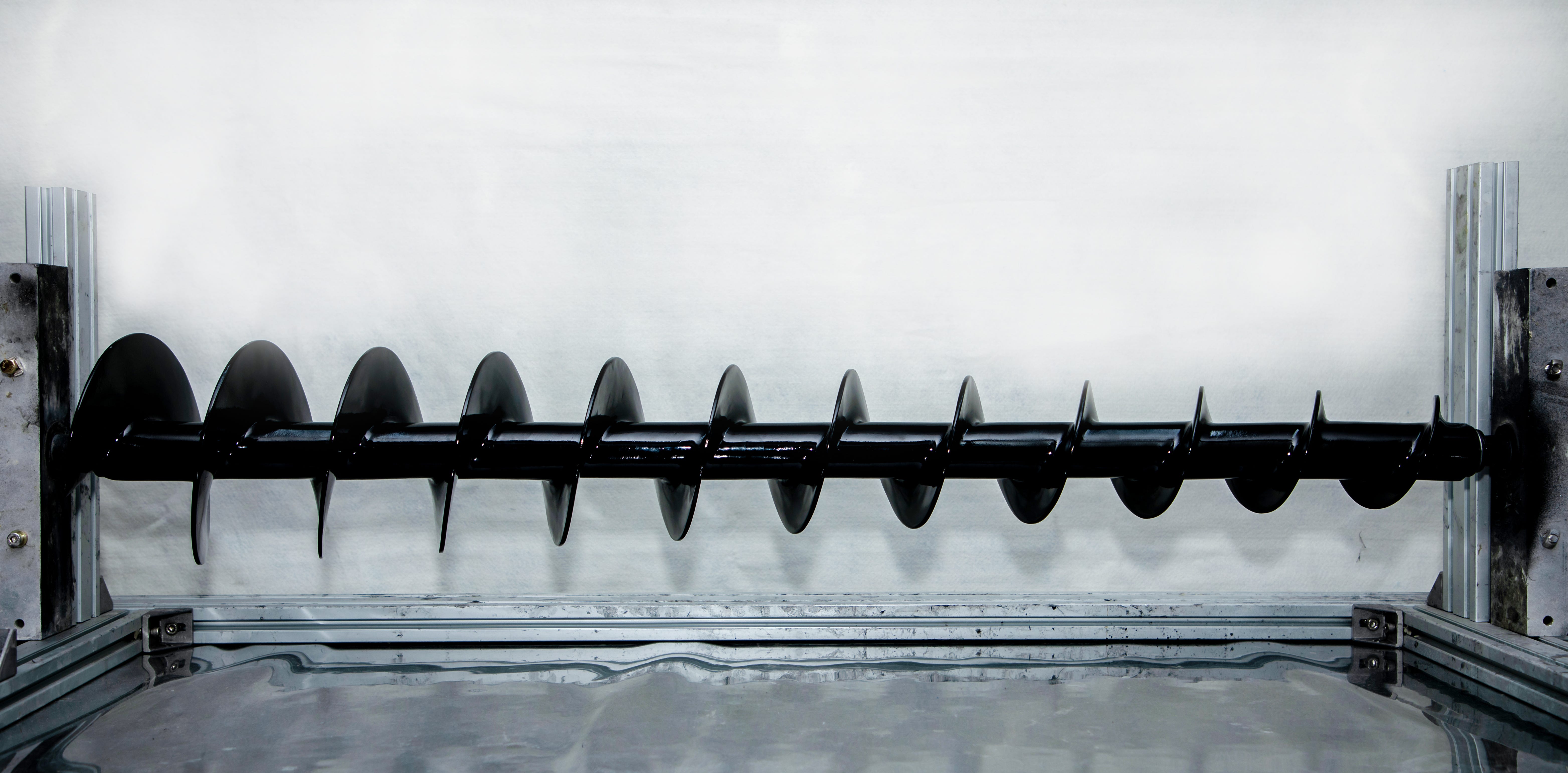
Fabheads Advantage
Fabheads’ Archimedes screws fare better than the traditional metal-based screws currently available in the market. Fabheads is currently the only company making carbon fiber-based Archimedes screws in India with 3D printing. With Fabheads’ carbon fiber Archimedes Screws, the following advantages are evident
- Improved lead time
- Weight reduction — At least 30% less than aluminum
- Optimized power consumption
- Precision — Better than sheet metal screws
- Cost advantage — Similar or less than aluminum
- Better strength and stiffness properties compared to aluminum
- Corrosion resistance — Being carbon fiber-based, the screws are ideal for a marine or humid environment
- Customizable — An in-house trimming and finishing set-up gives Fabheads the flexibility of manufacturing customized screws of different shapes and sizes to meet the customer’s requirement
- End-to-end services — Fabheads fabrication services undertake the entire end-to-end process from design to prototyping, testing, fabrication, and post-processing
Incorporating carbon fiber and 3D printing technology elevates this simple tool of ancient times to make it more efficient and suitable for present-day applications.
Fabheads takes up similar challenging and complex design and fabrication projects to help expand the usage of fiber-based composites. These are drones airframes, marine structures, robotic components, etc. Very often these projects are marked by every other composites’ fabrication agency as “not possible with composites”. Fabheads, with its in-house design and analysis team, in-house printer farm, and continuous fiber printing capability, has been able to design and fabricate the impossible.