What makes the shift to on-demand manufacturing inevitable?
Jul 20, 2021

There are many takeaways from this pandemic, the words like — change, disruption, and adapting to the ‘new normal’ will be the jargons used across all industries. With the peak in the number of cases, the hospitals faced a shortage in equipment. It was common across all countries that witnessed the first and second waves of Covid-19. To support the health care workers, the manufacturing companies had to adapt to a new model that would churn out more products, to meet the demand. The pandemic paves the way to consider on-demand manufacturing to curb the shortage. Especially, 3D printing in the additive manufacturing space can help companies transform digitally into an on-demand business model.
Throughout this discussion, we will focus on the following items
- Traditional Manufacturing vs On-Demand Manufacturing
- How does 3D printing boost on-demand manufacturing?
- Who are some well-known players that are using on-demand manufacturing?
- How can India benefit from on-demand manufacturing?
Traditional Manufacturing vs On-Demand Manufacturing
The basic principle of traditional manufacturing is to produce a given number of units within a period of time. It also focuses on keeping an inventory for unexpected shortages. Traditional manufacturing typically works around the reduction of unit cost by producing larger quantities.
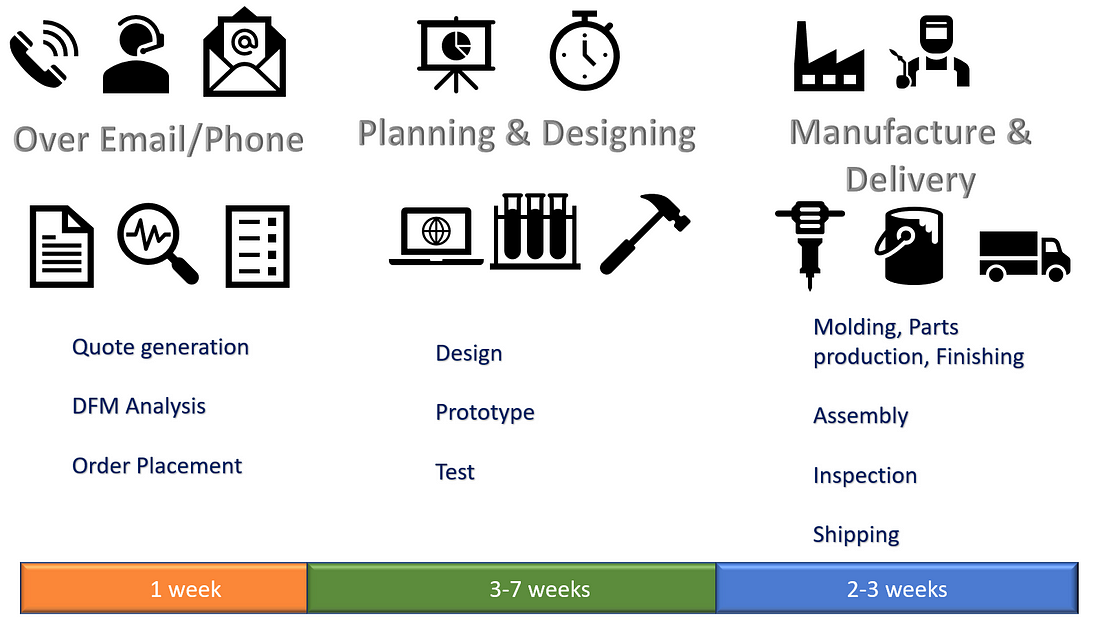
Traditional manufacturing involves —
- Requirement generation
- Production planning
- Production of large scale
- Storage & inventory management
- Delivery
All manufacturing systems have a buyer, an engineer, and a supplier. A buyer purchases the end product. The engineer designs and manufactures the product. The supplier is responsible for procuring the raw materials that are needed for production. In the traditional manufacturing process, there is a prolonged discussion on quoting the right price. The negotiations occur between the three parties to settle for a price that works for all. This is rather time-consuming.
Perhaps the biggest time-consuming factor is production planning. Elaborate factory plans, assembly lines, etc are planned to depend on the number of products to be produced. Even making molds and fixtures for processes like injection molding, robots for assembly, or item movement takes an enormous amount of time.
Another persisting issue is around inventory management. Predicting the number of units to be produced can be tricky. Especially for products with shorter shelf life, sometimes the inventory can go unsold. In such cases, manufacturing companies have no choice but to either sell these products at a discounted price or throw them away.
Coming to the customer interaction in the traditional manufacturing setup. The end-user is usually in the backseat. After initial quoting of price and payments. The customer is not in the picture. A customer has minimal involvement after the initial stages. This leaves a huge gap between the manufacturer and its end-user.
Now coming to the On-demand manufacturing model. The primary aim of this process is to consider customer feedback and deliver products in the shortest span of time. Instead of spending a huge chunk of time predicting the number of units to produce. They try to make the experience more user-centric. It utilizes digital platforms supported by cloud services to interact with its customer. Enabling a channel of communication with its customer allows them to generate quotes in real-time. The customer stays connected throughout the production process. The feedback is maintained during the manufacturing process. This incorporates, what we call the “Just-in-time” strategy which is common across various supply chains.
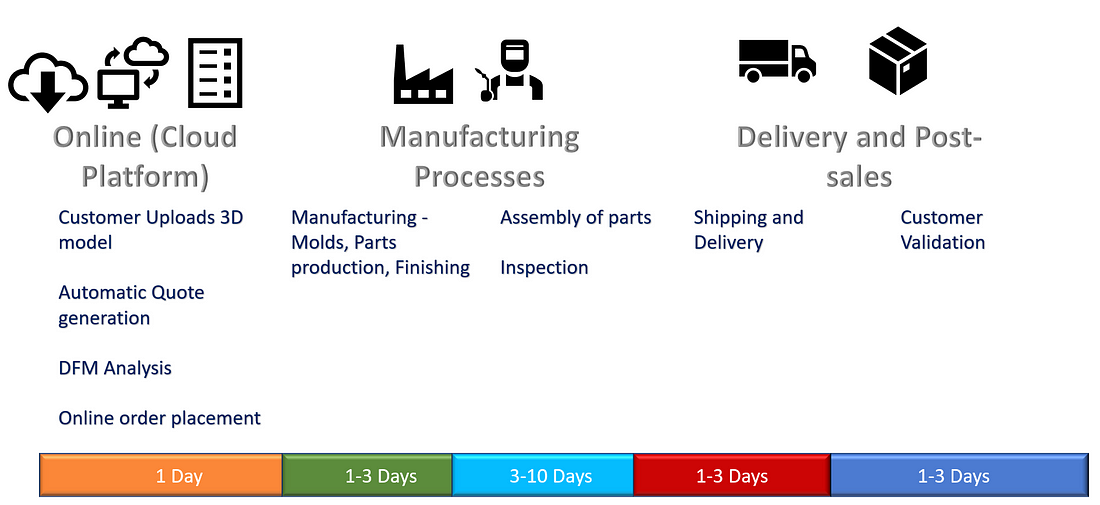
Let’s summarize and try to understand the differences of each system…
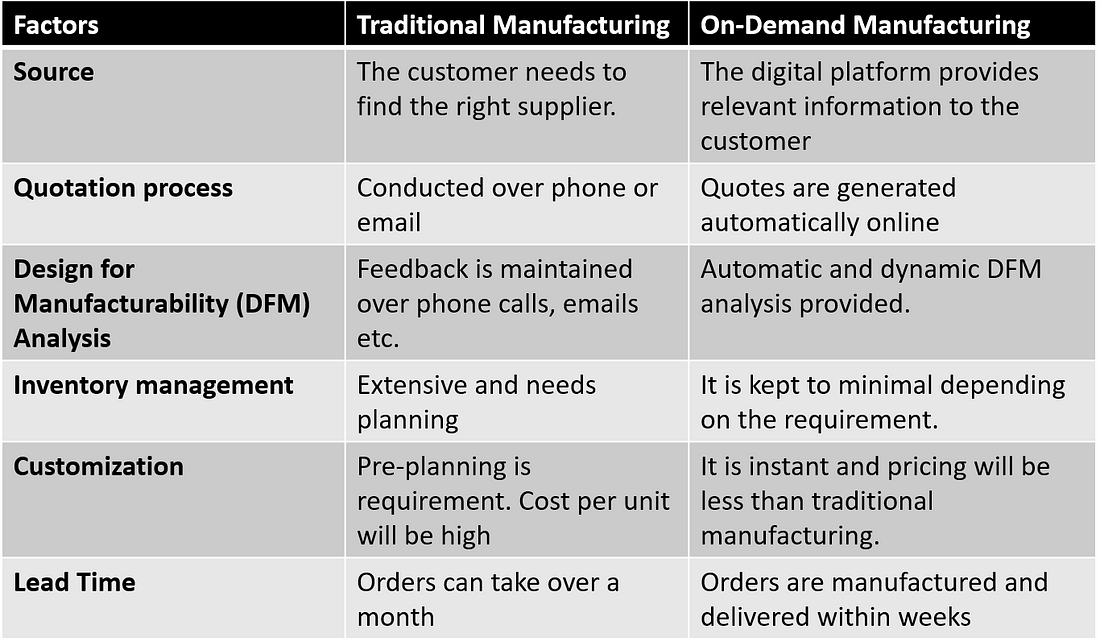
Now that we have looked closely at both the processes. We know that the large-scale productions in the traditional manufacturing system can be rigid and resistant to change. Most of the machinery in the traditional setup is pre-configured to manufacture in high volume. It requires more space for storage and maintenance in the inventory. However, the on-demand manufacturing approach focuses on reducing the lead time at every step of the production cycle. The flexibility in the process also allows customization (which would take a much longer time in a traditional approach). Another key point is to understand that modern-day technologies like 3D printing are more equipped to take on the on-demand approach versus the traditional approach.
How does 3D printing boost on-demand manufacturing?
Additive manufacturing techniques like 3D printing are adopting the on-demand manufacturing process at a rapid pace. It is easy for 3D printing to fit into a digital platform and deliver products to customers quickly.
3D printing itself is a digital process of printing objects. It requires a CAD model to be fed to the printer’s processing unit that converts the image into a 3-Dimensional figure. With the growth of 3D printing, the overall cost of its production has come down significantly. Hence, 3D printing and the on-demand manufacturing processes are complementary to each other.
“The situation is rapidly changing now, as on-demand manufacturing becomes ever more popular. 3D printing allows creating small series of products or parts quite cheaply.”
– Globalluxsoft
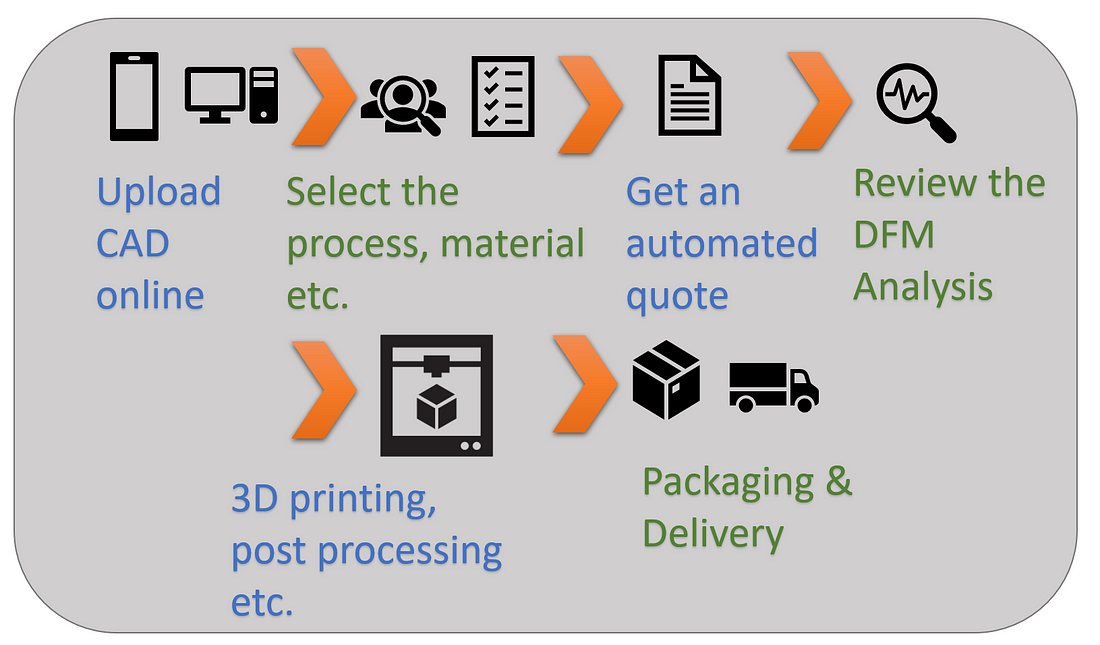
Several softwares aid in the execution of this model. Predictive analysis is often used to give accurate estimates to the customer. Thereby, reducing the lead time at the initial stage of the order placement. Customers no longer have to “fill out the form” to get to the quotation. The digitalization of the entire process from quote to manufacturing to delivery makes on-demand manufacturing a viable option. On-demand manufacturing and 3D printing result in a compact and customer-centric process with the following advantages:-
- The turn-around time is short
- Lead time is shortened (3D printing is relatively faster)
- Customer-centric approach
- The process is more agile (open to changes)
- Saves cost — both in terms of process and production
- No inventory storage required
- The online platforms make it accessible to a larger audience
- The process is transparent
- Easy to implement quality control procedures
On-demand manufacturing has become more common across various industries like — aerospace, automobile, etc. Let’s look into some big industries that have benefited from this method.
Well-known players using on-demand manufacturing
On-demand manufacturing can be lucrative, which makes it an attractive process. Here are some big players in the market that are making the best out of on-demand manufacturing.
Ford
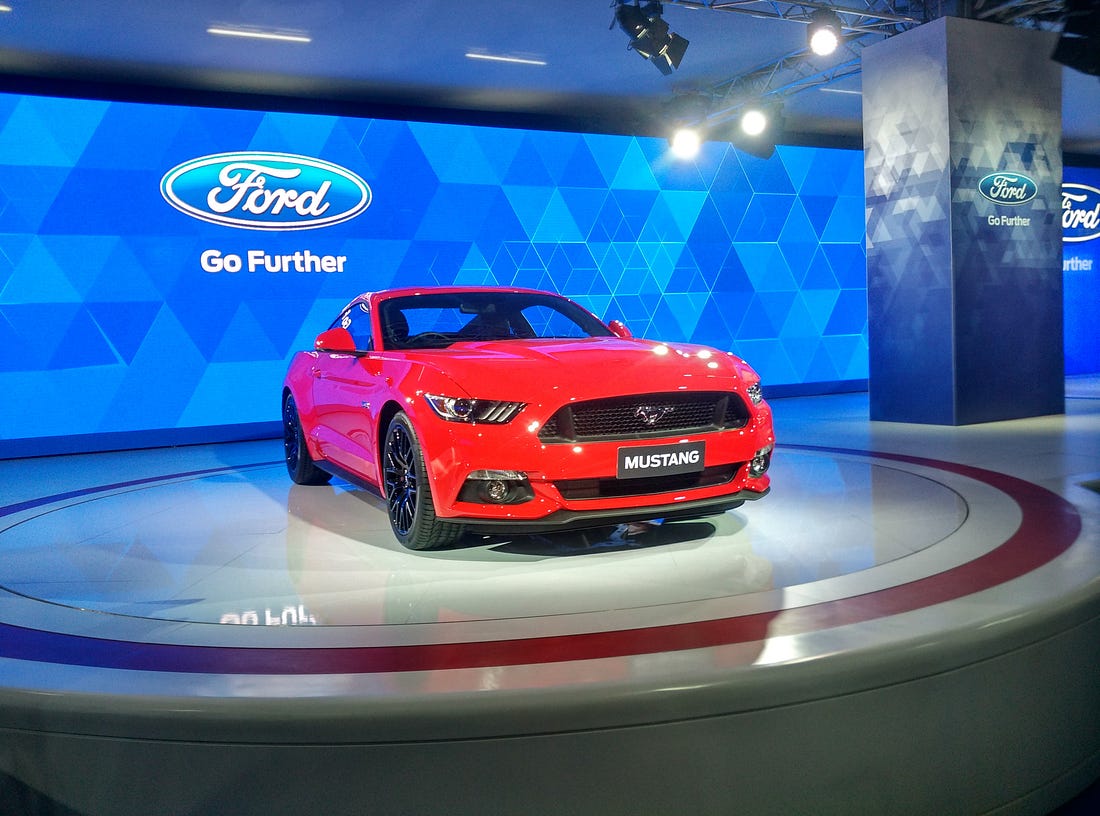
Eatch Licensed under CC-BY 4.0)
Ford uses 3D printing technology to print automobile parts. Typically, it takes about 5 months of lead time to produce prototypes of any parts in a traditional set-up. Using 3D printing, they can produce parts within a couple of days !! They use the on-demand manufacturing model, where customers can place orders in an online forum. Ford engineers are now able to cater to their customers more actively by enabling their services digitally. It offers services like spare parts production, repairs, etc.
“Consumers could also take advantage of this technology (3D printing) — downloading modifications or accessories to completely customize their vehicles”
– Itssupplychain.com on Ford’s Business Model
Electrolux
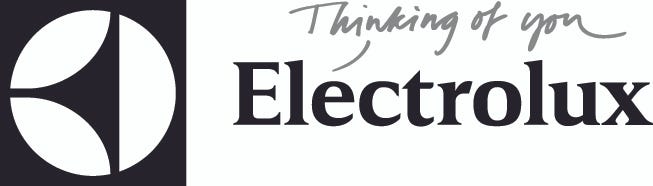
Electroluxis a Swedish company that manufactures home appliances like washing machines, vacuum cleaners, etc. It operates its business model using an on-demand manufacturing process to provide its customer with 3D printed spare parts. This helps them reduce costs at four levels —
- Manufacturing
- Inventory
- Maintenance
- Product Replacements
Caterpillar
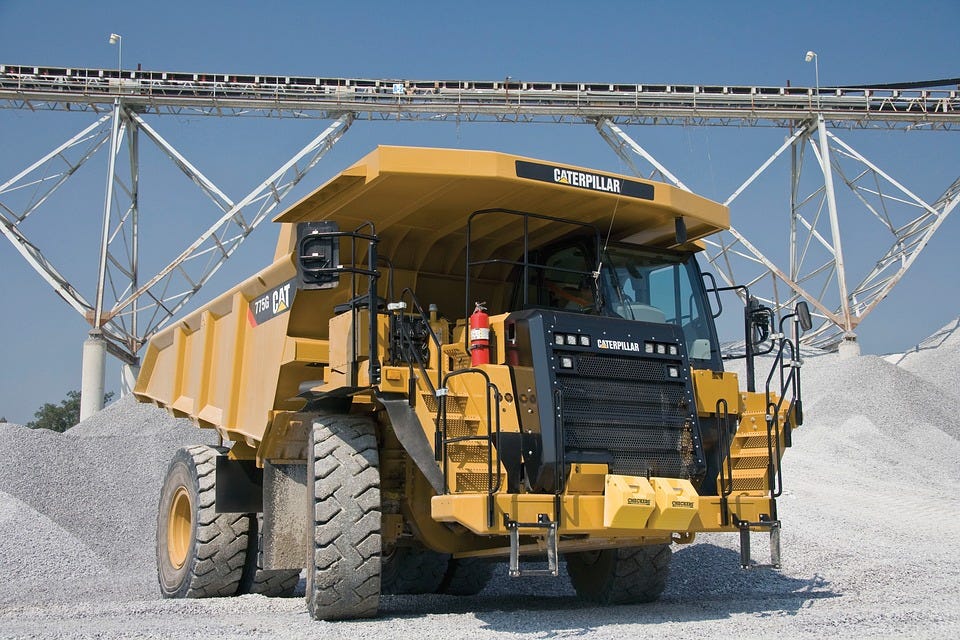
Caterpillar is one of the most popular construction companies that started using 3D printing in its day-to-day activities. They successfully print parts made out of aluminum and titanium. They have even printed an excavator from scratch. As an extension to the technological expertise, their business model caters to their customers through on-demand manufacturing. It is now looking to digitalize its process for some of its existing traditional manufacturing processes for the production of gas turbines, fuel mixers, etc.
Aerospace & Defense Industries in On-Demand manufacturing
The fourth industrial revolution also called — Industrial 4.0 process uses digital manufacturing and enables a smart ecosystem across different industries. The aerospace and defense industries are looking to seize the opportunity to transform themselves through multiple channels. Advanced manufacturing processes like 3D printing are gaining more traction as they can rapidly deliver on-demand and low-volume production.
Aircraft and rocket parts need not be mass-produced. They are often designed to specifications. Through digital AM (additive manufacturing) techniques, it is easy to customize and produce complex structures. Softwares are now able to consider additive techniques. CAD software allows engineers to work with innovative geometries and designs. Further, the focus is now more on what we discussed the “just-in-time” or on-demand manufacturing. Aerospace components are expensive. Hence, inventory management challenges are minimized through on-demand services. It cuts down the warehousing costs as well.
Lockheed Martin is a pioneer in the aerospace and defense industries. It uses the latest additive manufacturing techniques and drives on-demand manufacturing in its daily operations. They work with NASA and other defense companies to manufacture aircraft components, space vehicle equipment, rocket parts, etc.
“You have forgings which can traditionally take over a year to procure now able to be produced in an additive manner, with significantly less material waste, over a period of two weeks”
-Brian Kaplun, Senior Manager at Lockheed Martin
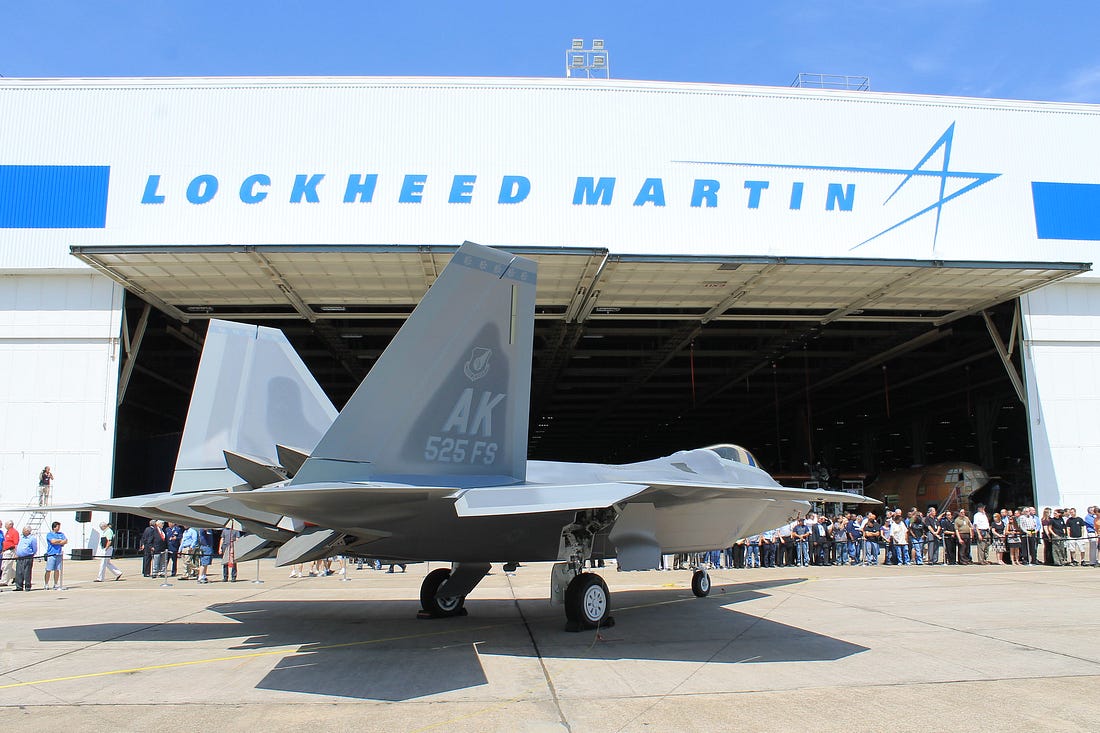
Charles Atkeison Licensed under CC BY 2.0)
The entire manufacturing industry is transforming in both technique and process. On-demand manufacturing is also accountable for the advancement in software technology. The progress in cloud service and virtual machines enables processes to transform digitally and rapidly. Many big companies in the world are speeding up production and delivery to give a hassle-free experience.
So far, we have looked at how 3D printing has helped on-demand manufacturing. Also, our discussion led us to get an idea about the real-world testaments that have embraced the transformation. It is now important to look at where India stands when compared to the rest of the world.
How can India benefit from on-demand manufacturing?
We can not deny that the manufacturing industry in India has suffered heavily due to the pandemic. However, businesses had to think on their feet and shift to a more digital mode of working. Many manufacturing companies had to detach themselves from the traditional methodologies and look at modern solutions. On-demand manufacturing pushes companies to automate their process at different stages. For example — Tata Steel works keenly on digitization of its process by adapting agile and efficient processes that enable on-demand manufacturing.
“Tata Steel in Kalinganagar, Odisha is one among 44 global elite facilities on the World Economic Forum’s Lighthouse Network of companies that have successfully combined digitization with the manufacturing process.”
– Article on industr.com
A new entrant into the world of manufacturing is a company called “Chizel.” They have a B2B online cloud service that is interactive and easy to use. Through the on-demand manufacturing model, they bring suppliers and manufacturers to a single platform.
“Digital manufacturing is the next leap for India’s tech leadership — the first being the software outsourcing movement in the 1990s.”
India has a great market to unleash some of the modern technologies and processes that help accelerate the growth of manufacturing industries. The idea is to build a system or a process is that can adapt to grave situations such as pandemics. On-demand manufacturing aided with 3D printing technologies can make manufacturing more robust. Many 3D printing companies, including Fabheads, were able to deliver face shields to the frontline workers due to their agile way of working.
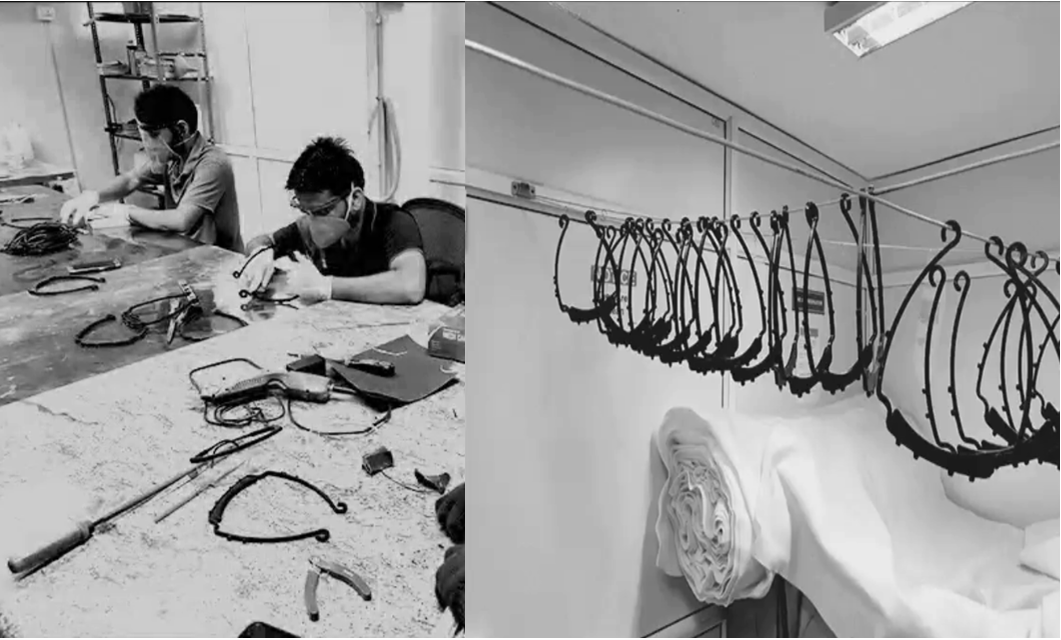
Conclusion
On-demand manufacturing is a fresh concept that has recently emerged in the manufacturing industry. It focuses on transforming the traditional process to help deliver customized products to the customers in a short time. Digital platforms based on cloud technology help facilitate the on-demand process effectively. On top of that, modern additive manufacturing techniques (3D printing) act as a catalyst to improve the overall customer experience in manufacturing goods. This article examined the potential of the on-demand manufacturing process by looking into —
- Comparison between traditional & on-demand manufacturing
- On-demanding manufacturing with additive manufacturing
- Companies that use on-demand manufacturing model
- The future of on-demand manufacturing in India
All in all, the new approach in manufacturing tries to improve the lead time and customer experience through a digitized supply chain.
Share your thoughts on-demand manufacturing in the comments below. Tell us if you think this model can transform the current state of manufacturing in India and the world.